A frequency inverter, mainly composed of a rectifier (AC to DC), filter, inverter (DC to AC), brake unit, drive unit, detection unit, micro-processing unit, etc., is a kind of electric control equipment, that uses frequency conversion technology and microelectronic technology to control AC motor by changing the working power frequency of the motor. With the continuous improvement of industrial automation, frequency drive inverters have also been widely used. The wide application of inverters is due to their powerful functions. Inverter.com will explain the advantages of inverters to you, hoping to be helpful to you.
The working principle of frequency inverters
In general, the frequency drive inverter adjusts the voltage and frequency of the output power supply by the breaking of the internal IGBT, and provides the required power supply and voltage according to the actual needs of the motor, to achieve the purpose of energy saving and speed regulation. In addition, the inverter also has many protective functions, such as over-current protection, over-voltage protection, over-load protection, and so on. With the continuous improvement of industrial automation, variable frequency inverters have also been widely used.
The figure above is a circuit with variable AC frequency. Among them, P and N are converter circuits, which can adjust AC to DC and load it to load Z. When the pulse signal to P is sinusoidal, the tuned DC is sinusoidal, which is the first half of the sinusoidal curve, and the period is the sinusoidal regular period of the pulse signal, which is an integral multiple of the AC period. Through the cooperation of P and N, the periodic sinusoidal current on load Z is formed, and the frequency can be adjusted according to the period of the pulse signal, which is the working principle of the frequency drive inverter.
Frequency inverter benefits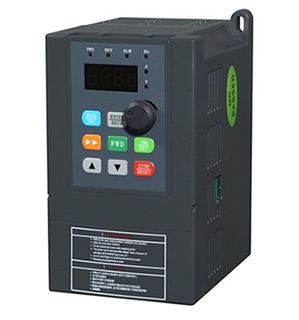
- Adjustable torque limit: After adjusting the speed by frequency conversion, the corresponding torque limit can be set to protect the machine from damage, so as to ensure the continuity of the process and the reliability of the product. At present, the frequency conversion technology makes not only the torque limit adjustable but also the control accuracy of the torque reach about 3%-5%. In the power frequency state, the motor can only be controlled by detecting the current value or thermal protection, but can not be operated by setting the precise torque value as in the frequency conversion control.
- Controllable stopping mode: Like controllable acceleration, the stopping mode can be controlled in the frequency control system and different stopping modes can be selected (decelerated parking, free parking, decelerated parking + DC braking). Similarly, it can reduce the impact on mechanical components and motors, thus making the whole system more reliable and prolonging the service life accordingly.
- Energy-saving: The energy saving of frequency inverters is mainly manifested in the application of fans and pumps. To ensure the reliability of production, all kinds of manufacturing machines have a certain amount of surplus when they are designed and equipped with power drives. When the motor fails to run under full load, it may not meet the requirements of power drive or excess torque increases the consumption of active power, resulting in a waste of electrical energy. For traditional equipment such as fans and pumps, the frequency control method is to adjust the air supply and water supply by adjusting the baffle and valve opening at the inlet or outlet, which has a large input power, and a large amount of energy is consumed in the process of closure by the baffle and valve. In the use of frequent control, when the flow requirement is decreased, the frequency control can be achieved by reducing the speed of the pump or fan.
- Reversible operation control: In the control of frequency inverter, there is no need for additional reversible control devices to realize reversible operation control, just change the phase sequence of output voltage, which can reduce maintenance costs and save installation space.
- Reduce mechanical transmission components: At present, vector control converter plus synchronous motor can achieve highly efficient torque output, thus saving mechanical transmission components, such as gearboxes, and ultimately constituting a direct frequency conversion drive system. Thus, the cost and space can be reduced and the stability can be improved.
To learn more about inverters such as single-phase output inverters, single-phase to three-phase inverters and single-phase to three-phase inverters, you can consult at inverter.com.